PO Matching is purely an internal business control, it is used to ensure that your company is paying the correct amount to your vendors for the quantity of goods or services received. Before delving into the specifics of 2-way, 3-way, and 4-way matching, it is important to have a conceptual understanding of the P2P (pay to procure) cycle.
The main benefit of automating your PO matching process is that it can help improve efficiency and accuracy. Automating 2-way, 3-way, and 4-way PO matching can help reduce errors and save time by eliminating manual data entry. In addition, automating your PO matching process can help improve visibility into your spend by providing real time data and analytics.
P2P Cycle Explained
Step #1 – Purchase Requisition – Typically, a purchase requisition is what kicks off the P2P cycle. A purchase requisition is filled out by an employee of the company, requesting, and specifying the necessity for select goods or services.
For example, let’s assume that one of the roles of a factory worker is to ensure that the factory always has 10,000kg of plastic on hand for manufacturing. The employee notices that the stock has fallen below 10,000kg, and therefore he fills out a purchase requisition and sends it to the purchasing department within the company.
Step #2 – Purchase Order – Upon receipt of the purchase requisition, the purchasing department will generate a purchase order. The purchase order will contain details about the transaction with the selected vendor such as Quantity, Price, Delivery Date, Purchase Order Number, Vendor Details, etc. The purchase order number will be shared with the selected vendor. The vendor, in turn, will then input this PO number on the invoice(s) they send in for these goods/services.
Step #3 – Receiving – After ordering the goods or services, the services will then be rendered by the vendor. In our example of ordering plastic for manufacturing, the receiving department within the company would receive and process the received delivery of goods. The receiving department will then generate a receipt of goods received, also known as a packing or receiving slip.
Step #4 – Inspection – The received goods are then inspected for quality. The number of goods that meet the company’s quality standards and the quantity sent back are then recorded on an acceptance or inspection document.
Step #5 – Invoicing – The Accounts Payable department will receive an invoice from the vendor, documenting things such as the quantity of goods or services, price per good/service, and PO number.
In addition, the AP department will also receive the receiving slip and acceptance document (if applicable). This is where the concept of 2-way, 3-way, and 4-way matching comes into play.
2-Way PO Matching
The 2-way PO match is the most common control in place for businesses and occurs when the AP Clerk compares the details of the purchase order (generated by the purchasing department in step #2) against the received invoice (step #5) from the vendor.
The most critical items that are compared are the QUANTITY BILLED with the QUANTITY ORDERED and the INVOICE PRICE with the PURCHASE ORDER PRICE.
3-Way PO Matching
The 3-way PO match incorporates all of the controls from the 2-way match, in addition to comparing the receiving slip (receipt) QUANTITY RECEIVED to QUANTITY ORDERED on the invoice.
4-Way PO Matching
The 4-way PO match incorporates all of the controls from the 3-way match, in addition to comparing the QUANTITY BILLED (invoice) to the QUANTITY ACCEPTED (inspection document).
P2P Cycle Explained (Cont.)
Step #6 – Pay – Once the AP department has validated that all of the information on the invoice is correct (via the 2, 3, or 4-way match), the invoice is then paid.
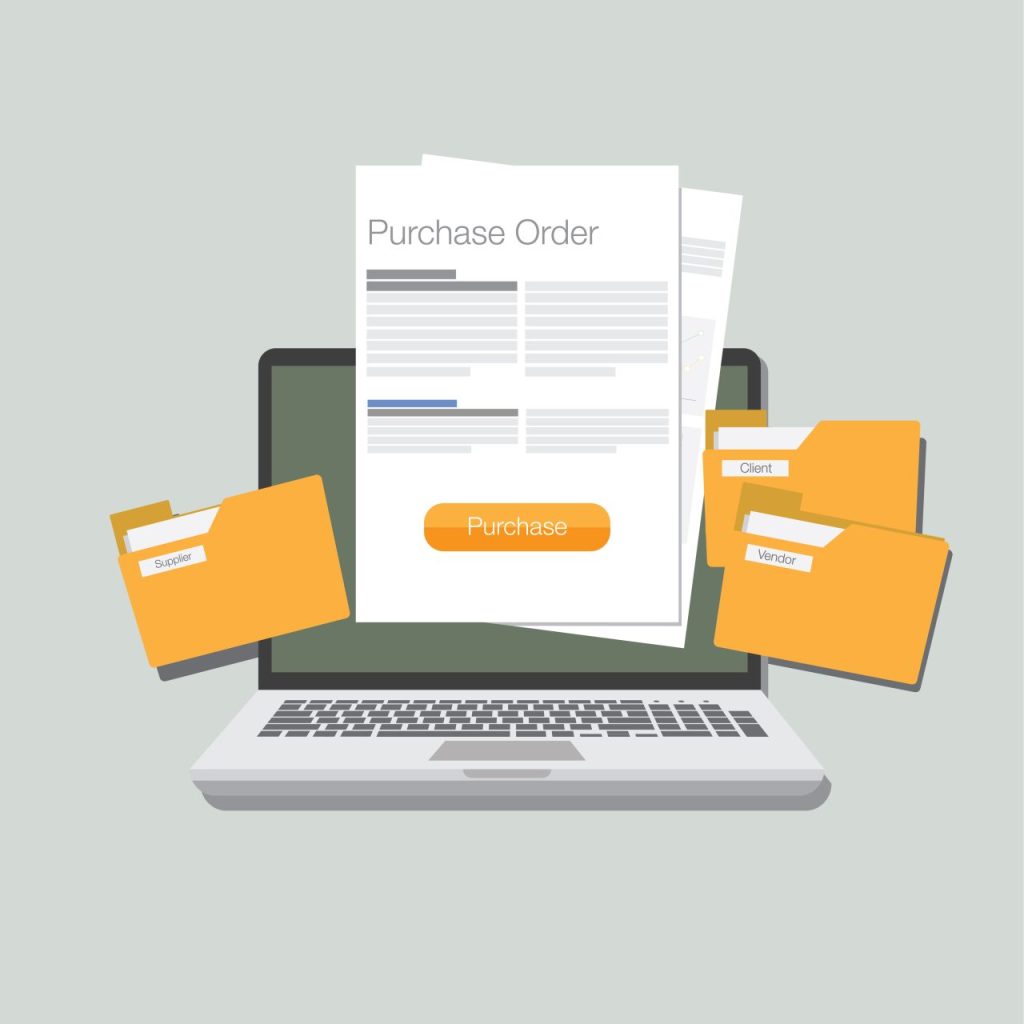
The Importance of PO Matching
PO Matching is a crucial control that all businesses should incorporate. While there are varying levels of complexity, each form of PO matching ensures that your organization is not paying for goods or services it did not receive. Multiple sources have estimated that approximately 2% of invoices paid are duplicates, among the many invoicing discrepancies that can occur. Picking the correct control to implement is often a factor of multiple things within your organization, such as size, complexity, sector, etc.
While the process of this control can be tedious and time-consuming, products such as EZ Cloud can vastly assist and expedite the PO process. EZ Cloud assists by placing all the relevant P2P data in front of the user with a single click. Without a digital and autonomous AP process, users are often left to locate and compare multiple streams of data from multiple P2P software platforms or pieces of physical paper.
Efficiency issues in the AP department can lead to multiple issues including, but not limited to— Loss of early pay discounts, late payments, lost invoices, over or underpaying owed amounts, high labor costs, communication issues, etc.
If your company is looking to implement quality controls into AP, the EZ Cloud team would love to show you how we can assist and enhance your process. Schedule a free discovery, consultation, and product demo here.